If you could cut labor costs by as much as 10 percent, would you do it?
Searching for tools and equipment is one of the biggest time wasters on a job site. Tracking down that drill you just had or searching for a ladder that should have been left on the job site cuts into productivity. Better tool management can stop that waste and save you a chunk in labor costs.
But tool-tracking is tedious, so it doesn’t always get done or done well. Tracking software can take the hassle out of the process so you’re wasting less time, and thus, less money.
The right tool-tracking software can improve operations immensely. Let’s look at how they work and what to look for when you’re ready to use one for your operations.
It’s All About That Process
Tool loss has more to do with your process than theft or carelessness. Unfortunately, many companies have made the process of tracking tools tedious and time-consuming. If you’re still trying to do this by using a Sharpie and spreadsheet, asset-tracking software can change everything for you.
Most contractors look at new technology as a way to help improve productivity with 42 percent planning to start using tool tagging by 2022 as one element of that effort.
Because construction tools move from site to site, they’re more mobile than most assets, which contributes to them being easy to lose. Their smaller size also makes it easier for them to walk off a site or just get buried in a toolbox or truck bed. Your process needs to include better inventory, tagging, and tracking management to save time and money.
Inventory the Tools
Everything starts with organization and that means a complete and accurate inventory list. Because tools move around a lot, this is tougher to do than you might expect unless you want to stop work.
Have each job site take an inventory of its tools so you have the list. You’ll need this list to assign tags for each tool and job site. Expect the inventory to grow as you work through the process since some of those lost tools are going to be missed in the original counts.
Once you have inventory lists, you need to ensure they are accessible to everyone. Not everyone needs to be able to change information, but they do need to be able to see and reference the list. This lets them confirm whether you have a tool before they buy a new one or get it transferred to the correct site.
Tag the Tools
Tagging has to move beyond writing a name on the handle with a marker. Today’s tracking software uses a combination of Bluetooth technology and mobile apps to locate tools.
Your system should provide small ID tags that can be attached to each tool. These are usually stickers with QR codes on them. Employees scan the tag with their phone, which updates your system with location, time, and date. This helps make sure that your tools get in and out more efficiently and in an accurate way.
Manual inventory can take two to three minutes per tool for writing down asset numbers and signing logbooks. Digitizing the process can cut that in half, and using Bluetooth and barcodes drops the time even more.
Track the Tools
Tracking happens within the main software, which should be cloud-based to enable workers at all sites to access it easily. This pushes responsibility for the tools into the field, which is where they’re most likely to get lost.
You’ll need to make sure all team managers, superintendents, and foremen have the app on a phone or tablet so they can access the inventory list. Workers then need to be able to scan to checkout or assign tools as needed.
Tracking should be helped along with a good categorization system that lets you sort and filter by tool type, job, and other features.
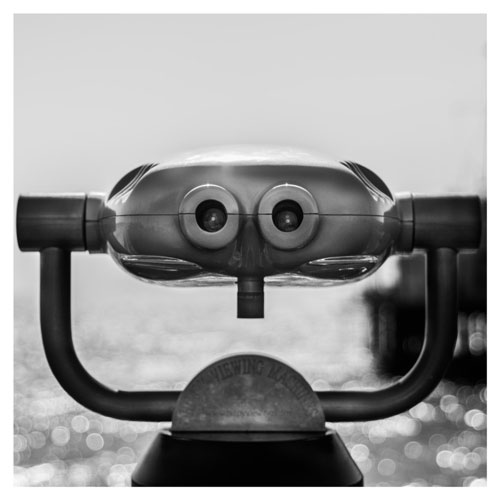
What to Look For in Tool-Tracking Software
Your tool-management system needs to bring together some key elements, most of which are tied to you using a cloud-based system. Construction has always been a remote job, but using the cloud for tracking means team members can have access to relevant information no matter where they are.
The most important part of this is the inventory list, which is updated in real-time so foremen on each job can see where tools are at all times.
You want a system that uses QR code technology to make checking tools in and out quick and easy. This allows you to run things on mobile phones and tablets so you don’t need to invest in specialized barcode scanners. This tech should allow you to assign each asset a randomized code.
Ideally, the system should be easy to use, available for multiple devices, and make it simple to check in or out multiple items at a time. You want to be able to see what you have, how many, where it is, and where it has been at a glance.
Your tool-tracking software should integrate with your project management software to help keep up with maintenance schedules, repairs, and purchase orders.
Get Tracking Today
A good management process serves as the basis for keeping up with your tools. Tool-tracking software can make that process work faster and more reliably since it doesn’t add work for your employees. You’ll know the tools you need are available and stop wasting time and money trying to track them down.
Interested in keeping your tools organized and knowing where they are at all times? Call us today at 800.458.7369 to talk to one of our experts about Sage ToolOps, powered by ToolWatch, and how it can improve your team’s efficiency, productivity, and overall bottom line.